What is a hydrocyclone with wear-resistant Rubber Liner?
Hydrocyclone is a device that separates slurry using centrifugal force. In its early days, it wasn’t widely adopted due to rapid wear, short equipment lifespan, and challenging control of process parameters. However, with the introduction of wear-resistant Rubber Liners in hydrocyclones, their lifespan significantly increased, gaining widespread acceptance and use in the market.
In this article, we will provide a detailed overview of wear-resistant hydrocyclones, covering their structure, working principles, specific functions, applications, common issues, and considerations.
I. Structure and Working Principles of Hydrocyclones:
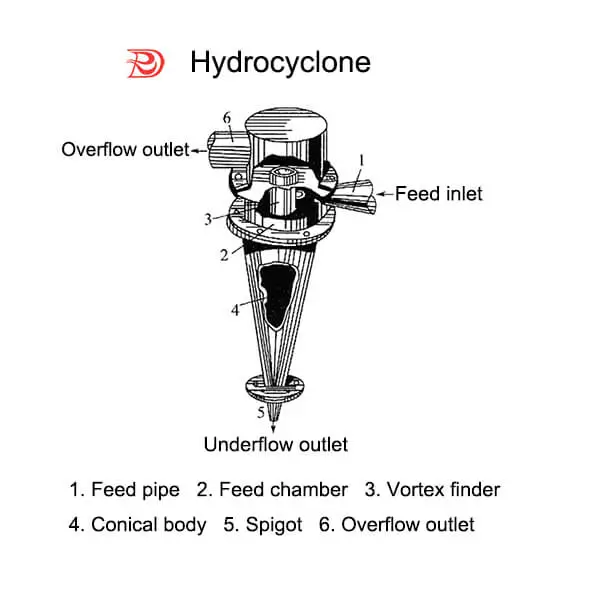
As depicted in the diagram, a hydrocyclone consists of a hollow cylindrical upper part and a conical lower part, forming the chamber. The upper part features a feed device, the top has an overflow device, and the bottom includes a sand outlet. These components are connected using flanges and screws. The inlet pipe, sand outlet, and the interior of the chamber are prone to wear. To address this, wear-resistant Rubber Liners, typically made of rubber, are added to these vulnerable areas.
The working principle of a hydrocyclone involves pressurizing the slurry (at 0.5-2.5 kg/cm²) and introducing it into the chamber at a velocity of approximately 5-12 meters/second. When the slurry, containing suspended solid particles, enters the chamber tangentially, the rapid rotation of the slurry forces it to follow the circular structure of the chamber. This rotation generates centrifugal force, causing particles with larger sizes to overcome water resistance better due to their greater inertia. Consequently, during continuous rotation, particles of different sizes and water form layers due to their varying centrifugal forces and gravity, achieving the separation of slurry components.
II. Functions and Applications of Hydrocyclones:
- Particle Separation Operations:
• Particle Grading: Separates particles with similar densities based on size, dividing them into coarse and fine particles or removing either category from the product. Often, multiple hydrocyclones are used to improve accuracy.
• Particle Sorting: Separates particles based on their density, utilizing either heavy-medium or water-medium hydrocyclones.
For instance, a plant with a slurry containing 160-200g/L solid content, where +100 mesh particles constitute 53% and -200 mesh particles are 37.4%, uses hydrocyclones. After processing, the overflow product contains 96% -100 mesh particles, while the underflow contains over 85% +100 mesh particles. - Concentration Operations:
Hydrocyclones concentrate materials by dewatering, enabling pre-concentration and reducing the load on subsequent equipment. Concentration rates of over 50% in the underflow and over 70% in production yield can be achieved. Hydrocyclones often work in conjunction with vacuum filters, screening machines, dewatering machines, and thickeners, replacing large, costly gravity sedimentation devices.
For example, in tailings processing at a mine, a system comprising hydrocyclones, thickeners, and dewatering screens concentrates the slurry to under 15% water content. - Clarification Operations:
Hydrocyclones remove dispersed phase materials from liquids, ensuring clean fluids. Proper adjustment of structural parameters, such as diameter and cone angle, according to the dispersed phase material’s size and density difference, is vital for effective clarification. Filtering before the hydrocyclone can reduce clogging.
In a chemical plant filtering a slurry with CaCO3 and dust particles, hydrocyclones efficiently remove particles below 15μm, achieving a separation rate of 70%-85%.
Hydrocyclones are increasingly diverse in structure and application. They can be used in series for finer product separation, in parallel for increased yield, or in combinations to optimize traditional dewatering processes. They find applications in mining, papermaking, construction, chemistry, and other fields.
III. Factors Affecting Hydrocyclone Efficiency:
- Diameter: Larger hydrocyclones generally have higher efficiency.
- Cone Angle: A larger cone angle increases flow resistance, leading to lower efficiency.
- Inlet Pipe Diameter: Larger inlet pipes enhance efficiency.
- Overflow Pipe Diameter: With constant chamber pressure, larger overflow pipes increase efficiency.
- Inlet Shape and Size: The shape and size of the inlet affect the hydrocyclone’s efficiency.
- Underflow Outlet Diameter: Larger outlets produce finer classification; they also improve efficiency.
- Internal Wall Roughness: While internal wall roughness minimally impacts efficiency, using DEF Rubber’s wear-resistant Rubber Liners enhances efficiency.
- Slurry Viscosity: The viscosity of the inlet slurry affects hydrocyclone efficiency.
- Ratio of Underflow Outlet Diameter to Overflow Outlet Diameter (Cone Ratio): Higher cone ratios lead to finer classification, but efficiency decreases.
However, high efficiency isn’t the sole criterion when selecting hydrocyclones. Users must consider both their production requirements and desired separation results.
IV: Common Issues with Hydrocyclones and Improvement Suggestions:
- Eliminating and Improving Short-Circuit Flow in Hydrocyclones:
To control short-circuit flow, modifications to the overflow pipe structure are crucial. Approaches include creating a circular short-circuit flow outlet between the top cover and overflow pipe and adding circular teeth to the overflow pipe’s outer wall. Practical applications have shown that implementing these changes can improve classification efficiency by 8% and increase separation precision by 1.8 times. - Eliminating and Improving Air Columns in Hydrocyclones:
Air columns negatively impact the separation process. Solid rods occupying the previous air column space can effectively eliminate air columns. Practical tests indicate that incorporating solid rods reduces internal losses by an average of 51.5%. However, adding central solid rods reduces the hydrocyclone’s overflow volume. - Improving the Flow Structure at the Hydrocyclone Inlet:
The flow structure at the hydrocyclone inlet, caused by redirection and expansion, leads to energy losses and turbulence. Hydrocyclones with curved inlet structures effectively mitigate these issues, significantly enhancing separation efficiency.
In conclusion, this comprehensive overview provides insights into wear-resistant hydrocyclones, from their construction and operational principles to their diverse applications and efficiency improvement strategies. For further inquiries about hydrocyclones and Rubber Liner solutions, please feel free to contact DEF Rubber.