How Does a Hydrocyclone Work?
Hydrocyclones are crucial equipment used in various industries for separating particles from liquids. Understanding how a hydrocyclone works can help optimize its use and maintenance, improving operational efficiency. At DEF Rubber, we provide high-quality custom hydrocyclone parts that offer excellent durability and performance, effectively replacing traditional brands like Linatex rubber without compromising quality.
- How Does a Hydrocyclone Work?
- Types of Hydrocyclones
- Components of a Hydrocyclone
- Applications of Hydrocyclones
- Common Issues and Solutions in Hydrocyclone Operation
- DEF Rubber’s Hydrocyclone Parts: The Perfect Alternative
- Contact DEF Rubber for Your Hydrocyclone Needs
1. How Does a Hydrocyclone Work?
A hydrocyclone separator operates based on the principle of centrifugal force. When slurry is injected into the hydrocyclone tangentially (through the feed pipe), it creates a rotating vortex. The centrifugal force causes particles of different sizes and densities to follow different trajectories. Larger and denser particles are pushed toward the walls of the cone, where they exit through the underflow, while finer and lighter particles move toward the center and exit via the overflow.
The basic operation trajectory is illustrated below:
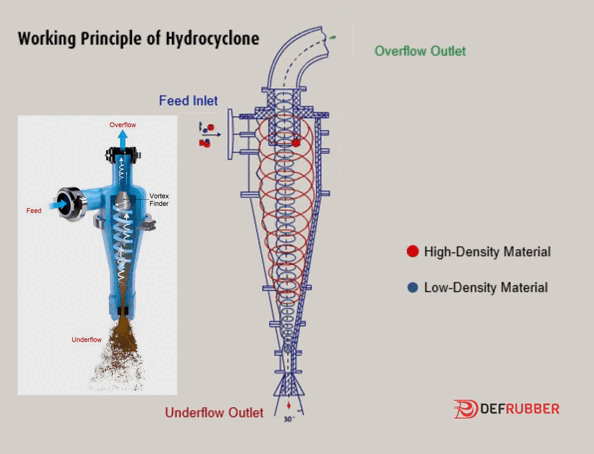
- Coarse and high-density particles exit via the underflow port.
- Fine and low-density particles exit via the overflow port.
This separation process enables the efficient classification of particles by size and density, making hydrocyclones widely used in mineral processing, water treatment, and many other applications.
2. Types of Hydrocyclones
Hydrocyclones come in various types, each designed for specific applications. Common types include:
- Deoiling Hydrocyclone: Used for separating oil from water.
- Desanding Hydrocyclone: Primarily used for removing sand or fine particles from water.
- Dewatering Hydrocyclone: Specially designed to remove excess water from slurry.
Each type is designed to address specific separation requirements based on particle size, density, and the fluid’s composition.
3. Components of a Hydrocyclone
A typical hydrocyclone separator consists of the following main components:
- Body (Shell): The main chamber where separation occurs.
- Feed Inlet: Where the slurry enters the hydrocyclone.
- Overflow and Underflow Ports: Channels for fine and coarse particles to exit.
- Vortex Finder: Directs the flow of the slurry within the hydrocyclone.
- Spigot (Apex): Controls the underflow discharge rate.
Properly adjusting the depth of the overflow pipe, cone angle, and feed pressure can optimize the performance of the hydrocyclone and enhance separation efficiency.
4. Applications of Hydrocyclones
Hydrocyclones have broad applications across various industries, including:
- Oil & Gas: For separating sand from drilling mud and oilfield fluids.
- Mineral Processing: Used in mineral classification, tailings thickening, and desliming processes.
- Water Treatment: To remove particles and grit from water.
- Food Processing: Separation of solid particles from liquids.
- Chemical Processing: Used for filtration and separation in various chemical processes.
5. Common Issues and Solutions in Hydrocyclone Operation
While hydrocyclones are highly efficient, certain issues can affect their performance. Here are some common problems and solutions:
- Airlock in the Pump: Can cause instability in the slurry flow. Solutions include adjusting pump speed or adding a return pipe.
- Underflow Blockage: Blockages at the underflow port can impede flow. This can be fixed by using larger spigots or cleaning the internal flow path.
- Poor Underflow Concentration: Ensure the underflow concentration meets process requirements by adjusting feed pressure or replacing worn-out components.
- Overflow Contaminated with Coarse Particles: If the overflow carries large particles, check the overflow pipe diameter and feed pressure.
- Excessive Wear: Hydrocyclones are subject to wear at the underflow spigot and cone areas. Using wear-resistant materials and optimizing the internal design can help minimize this.
6. DEF Rubber’s Hydrocyclone Parts: The Perfect Alternative
DEF Rubber manufactures custom hydrocyclone parts that provide excellent performance, superior durability, and cost-effectiveness. Our products are designed to replace conventional brands like Linatex rubber without compromising on quality.
Why Choose DEF Rubber Parts?
- Superior Wear Resistance: Our materials outlast competitors, offering up to 3x longer service life in high-abrasion environments.
- Cost-Effective: We offer custom-made parts that eliminate the premium costs associated with branded products.
- Easy Installation: Our parts are designed to seamlessly fit into your existing hydrocyclone systems, providing a hassle-free replacement option.
- Customization: Whether for Cavex hydrocyclones or FLSmidth/KREBS systems, we offer custom hydrocyclone parts tailored to your specifications.
Learn more about our custom hydrocyclone parts and replacement solutions.
7. Contact DEF Rubber for Your Hydrocyclone Needs
If you’re looking for high-performance hydrocyclone spare parts that deliver cost savings without sacrificing quality, DEF Rubber is here to help. Our products are built to optimize your hydrocyclone systems, improving efficiency and reducing maintenance costs.
👉 Contact us today for a quote or consultation on custom-made hydrocyclone parts.